Spotfire powers your smart factory
Whether you’re a process, yield, or test engineer, fab manager, or in supply chain management, you face daily challenges like increasing costs, disrupted supply chains, strict compliance, and changing customer demands.
Get smarter solutions with Spotfire, a visual data science platform that helps you reduce costs, improve operations, and increase profitability. With Spotfire for Manufacturing, you can identify production bottlenecks, detect quality issues, and predict machine failure—making your smart factory, even smarter.
Visual data science for manufacturing
Enhance production yield by uncovering hidden insights
With Spotfire, you can increase production efficiency, reduce waste, and save costs. Spotfire for Manufacturing uncovers hidden insights in your data—allowing you to address production issues and improve product quality. Provide data-driven insights to your engineers and managers to improve the decision-making process. With Spotfire, you can adapt to fast-changing market demands, reduce the development of new products and processes—and ultimately, increase your competitive edge.
Leverage visuals and data science to improve efficiency
Spotfire provides clear and intuitive representations of complex data at speed. Predict equipment failures and maintenance needs based on historical data to reduce unexpected breakdowns, extend equipment life, and decrease maintenance costs. Spotfire for Manufacturing maximizes the uptime of your factory and increases operational efficiency.
Drive innovation and take proactive measures
Enhance product development, support strategic planning, and improve operational decisions with Spotfire. Rapidly identify and adjust to market trends with cutting-edge visual data science. Spotfire allows you to share insights across the organization, fostering better teamwork and cross-functional collaboration. Visualize your data science to understand the root causes of failures, identify areas for improvement, and take proactive decisions to enhance product quality and reliability.
Spotfire empowers leading manufacturers
Brembo accelerates to improved processes with analytics
25% revenue increase with improved production efficiency
With Spotfire for Manufacturing, Brembo can analyze process optimization control, purchasing, quality control, and R&D data.
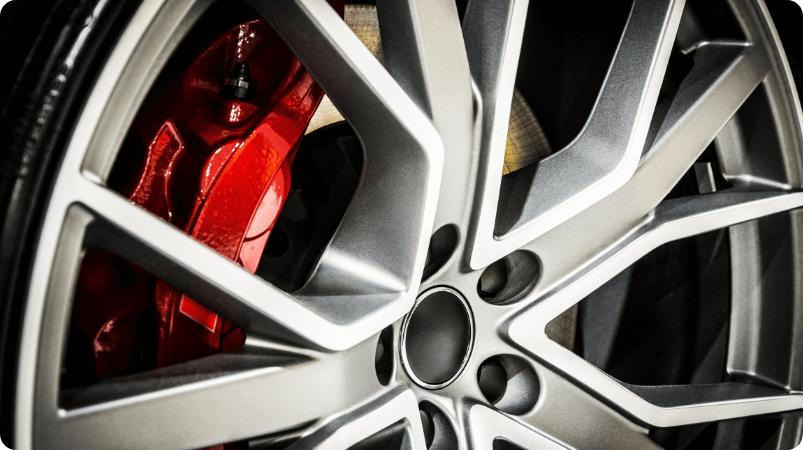
Discover more resources
AI-powered manufacturing solutions
Visual data science for manufacturing
By providing insights into production yield, bottlenecks, and root causes affecting quality, AI-powered Spotfire solutions empower organizations to optimize processes and improve efficiency.
World-wide excellence in manufacturing
Hemlock Semiconductor optimizes outputs and lower costs
$300K savings per month in electricity consumption via analytic-driven asset utilization
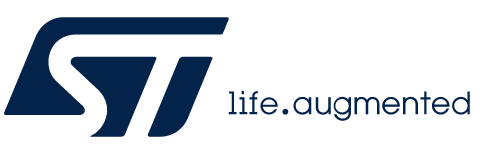
STMicroelectronics maximizes operational efficiency with Spotfire
1,500+ reports developed and in production

Keysight Technologies improves customer satisfaction with analytics-based product insights
Seconds for data loading versus hours