Spotfire empowers semiconductor engineers
In semiconductor manufacturing, every decision matters. Whether you're a process engineer, yield engineer, test engineer, or fab manager, your role is vital in tackling challenges such as maximizing equipment uptime, minimizing defects, ensuring consistent product quality, and optimizing production yield.
Spotfire is the visual data science platform built to empower professionals like you. By transforming complex technical data into actionable insights, Spotfire enables your team to make faster, smarter, and more impactful decisions—unlocking the full potential of your operations.
Visual data science for semiconductors
Accelerate process development and equipment efficiency
Managing process complexity and ensuring tool stability across hundreds of steps can be overwhelming. Spotfire streamlines root cause detection by bringing together process parameters, sensor data, and metrology data in one powerful visual analytics environment.
- Rapidly identify anomalies in high-dimensional process data
- Characterize and optimize module performance with confidence
- Ensure tight control of critical parameters to reduce variation and boost yield
- Eliminate time-consuming manual analysis and gain faster insight from every wafer
Uncover yield-impacting patterns
Speed and precision are everything. When performance drops or anomalies emerge, uncovering the root cause across millions of data points is critical. Spotfire empowers engineers to classify wafer signatures, correlate spatial patterns, and trace them back to equipment, process, and time-based data—so investigations lead to action, not dead ends.
- Detect and visualize spatial yield anomalies in seconds
- Correlate defect signatures with processing tools and steps
- Rank and prioritize excursions with statistical commonality analysis
- Build and use models of yield and performance

Fast, insight-driven reliability testing
Balancing cost, coverage, and quality isn’t optional—it’s a must. From early product characterization to root cause failure analysis, the pressure to deliver robust, reliable devices under tight timelines is relentless.
- Perform shmoo analysis across temperature, voltage, and frequency sweeps
- Rapidly identify marginal or failing behaviors under stress conditions
- Analyze test results and failure signatures across device families
- Reduce test time while improving product confidence and yield
From code to actionable insights
In semiconductor manufacturing, data scientists don’t just build models—they unlock engineering innovation. But models and algorithms built in isolation often fail to scale across teams.
- Embed R/Python models as reusable analytics functions
- Create enterprise-ready applications from one-off scripts
- Support cross-functional use cases—from predictive maintenance to yield optimization
- Focus on the algorithm—let Spotfire deploy the application for you
Empowering the top manufacturers

Hemlock Semiconductor uses Spotfire to optimize outputs and lower costs
$300K savings per month in electricity consumption via analytic-driven asset utilization
With Spotfire for Manufacturing, Hemlock Semiconductor can manage energy demand in real time, increase product quality, and detect production anomalies.

Discover more resources
Spotfire in action
Improve operations and production
Quickly identify the root cause of systematic yield loss with Spotfire. This demo shows how engineers use interactive wafer maps, spatial signature analysis, and equipment history correlation to detect anomalies and trace issues back to specific tools or process steps.
No coding required—just fast, visual, and powerful insights to keep your production running at peak performance.
Worldwide excellence in manufacturing
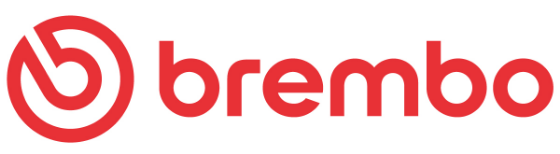
Brembo improves processes with manufacturing analytics
25% revenue increase with improved production efficiency
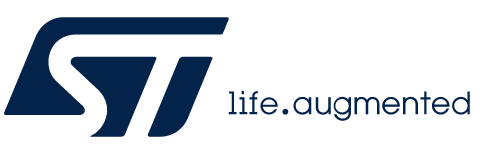
STMicroelectronics maximizes operational efficiency with Spotfire
1,500+ reports developed and in production

Keysight Technologies improves customer satisfaction with analytics-based product insights
Seconds for data loading versus hours