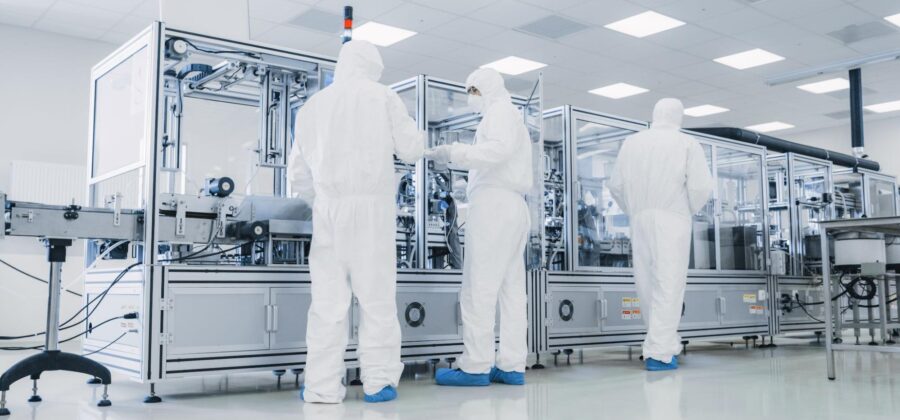
In the race to innovate, is your analytics platform holding you back?
In semiconductor manufacturing, success hinges on speed, precision, and the ability to see what others miss. Yet, many companies still rely on outdated, siloed analytics tools that slow progress instead of fueling it. When navigating complex data from multiple systems—MES, defect inspection, test data, and more—basic business intelligence won’t cut it.
That’s where Spotfire shines. Purpose-built for the most demanding data challenges, Spotfire is a visual data science platform that delivers real-time insights, intuitive visualizations, and advanced analytics, helping semiconductor leaders think faster, act smarter, and stay ahead.
Traditional analytics tools fall short in semiconductor environments
Semiconductor operations depend on real-time precision and nuanced insights, and traditional analytics platforms simply don’t provide what is needed. Tools designed for generic business intelligence weren’t built with the complexity of wafer processes, defect analysis, or multivariate engineering data in mind. Instead of accelerating innovation, they often become roadblocks.
General-purpose BI tools lack depth and speed
Popular business intelligence platforms excel at producing visual reports and dashboards for business users, but they fall short in semiconductor settings. These tools were not designed to handle the massive data volumes and streaming inputs typical in fab environments. They can’t easily process time-series data or enable the inline statistical modeling needed for deep process analysis. For engineers who need to run multivariate correlations, monitor chamber-to-chamber variability, or detect early signals in yield loss, these tools often prove too slow and shallow.
Specialist tools are siloed and hard to scale
Semiconductor manufacturers often deploy specialized systems for yield management or process control. While these tools offer deep domain functionality, they’re typically isolated from other data sources. Each system holds part of the puzzle—MES data here, test data there, defect images somewhere else—making it hard to form a complete picture. These platforms also require advanced expertise to configure and maintain, limiting their accessibility and slowing down analysis when teams need to move quickly.
Fragmented insights and missed opportunities
When teams are forced to jump between tools or rely on analysts to translate data from one system to another, momentum is lost. Opportunities for optimization go unnoticed, root cause investigations are delayed, and insights stay locked away in silos. Without a unified analytics environment, semiconductor organizations risk making critical decisions based on incomplete or outdated information.
Spotfire is different: Built for complexity, made for everyone
Spotfire goes beyond traditional dashboards to deliver a platform optimized for the full semiconductor data lifecycle. Here’s how:
Unified data integration for holistic insights
Spotfire connects to a wide range of data sources relevant to the semiconductor industry—combining structured and unstructured data into a single, cohesive view. This enables comprehensive analysis across the fab.
Advanced analytics and AI-driven recommendations
Whether it’s wafer mapping, defect clustering, or predictive maintenance, Spotfire empowers users with a GenAI extension, native support for R and Python, and one of the world’s largest libraries of advanced algorithms through Spotfire® Data Science. Its AI-powered Recommendations Engine suggests visualizations and insights, accelerating discovery without slowing down workflows.
Visual data science for all
Spotfire democratizes analytics across your fab. Engineers, analysts, and business leaders can explore data on an intuitive analytics platform, and no coding is required for core analysis. Need advanced modeling? Simply integrate your Python or R scripts right within the Spotfire interface to create a reusable data function.
Scalable, enterprise-grade performance
Spotfire supports thousands of global users, offering robust security, compliance, and governance features. Whether deployed on-premises, in the cloud, or in a hybrid setup, Spotfire scales to meet the unique demands of high-tech manufacturing.
Real business value at every step of the process
Spotfire doesn’t just help you see your data; it helps you act on it. Semiconductor leaders rely on Spotfire to:
- Accelerate decision-making: Real-time data and AI recommendations streamline analysis, helping teams respond to yield issues, process drift, or equipment failures faster.
- Improve yield and reduce costs: By enabling deeper insights into defect patterns, equipment matching, and process variability, Spotfire supports higher yields and lower production costs.
- Foster collaboration and innovation: Break down silos between process, yield, and product engineers. With shared, interactive data applications, teams can co-create solutions, test hypotheses, and drive continuous improvement.
Why semiconductor leaders choose Spotfire
Spotfire is trusted by the top semiconductor manufacturers for a reason. Unlike other platforms, Spotfire empowers your teams to think without limits—offering the tools, flexibility, and speed you need to solve complex problems with confidence.
So, why settle for static reports when you can unlock a world of insight?
Ready to see how Spotfire can transform your semiconductor operations? Experience the platform built for your data and your industry today.