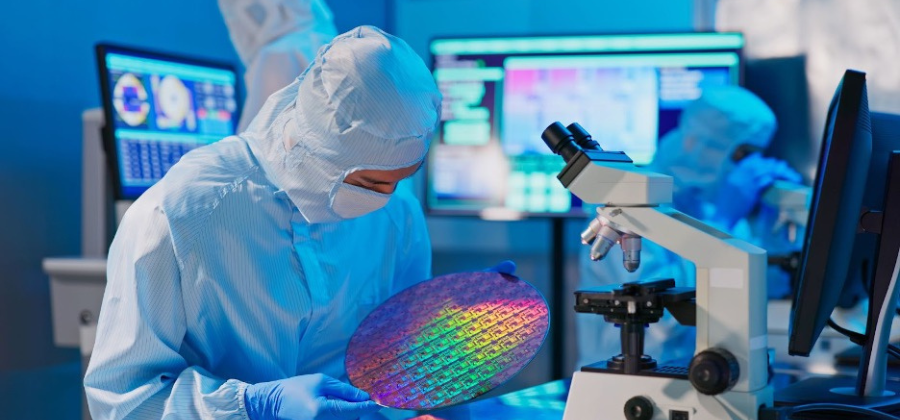
In semiconductor manufacturing, even a fraction of a percent increase in yield can translate into millions of dollars in savings. With the complexity of wafer fabrication, photolithography, etching, and testing—manufacturers must navigate vast data landscapes to identify process inefficiencies, detect defects early, and optimize performance. Traditional tools often fall short, making it difficult to pinpoint the root causes of yield loss.
Spotfire transforms this landscape with a powerful visual data science platform providing AI-powered recommendations, real-time analysis, and predictive analytics. By simplifying data complexity, Spotfire helps semiconductor companies maximize yields and minimize production costs.
Challenges in semiconductor yield optimization
Yield optimization in semiconductor manufacturing presents several unique challenges, from handling complex data to overcoming the limitations of traditional tools. Understanding these obstacles is key to unlocking efficiency and profitability.
Navigating complex semiconductor processes
High-mix, high-volume production environments involve thousands of variables influencing yield. From material properties to equipment performance, manufacturers must correlate data from disparate sources, including MES systems, defect inspection, and equipment telemetry.
Limitations of traditional yield management tools
Many legacy systems are rigid and siloed, restricting ad hoc analysis and requiring time-consuming manual data wrangling. The fragmented nature of these tools makes it difficult to detect subtle yield-impacting variations in real time.
The financial cost of inefficiencies
Yield losses result in wasted materials, increased rework, and production delays. A delay in detecting defects or process inefficiencies can cause substantial financial setbacks, impacting profitability and competitiveness.
How Spotfire drives yield optimization: Visual data science in action
Spotfire offers a transformative approach to yield optimization by integrating real-time data visualization, AI-powered recommendations, and advanced analytics. Here’s how it helps semiconductor manufacturers gain a competitive edge.
Unified data integration for holistic yield analysis
Spotfire seamlessly connects to various semiconductor data sources, enabling manufacturers to correlate process parameters with yield performance. By breaking down data silos, Spotfire uncovers hidden patterns and relationships that traditional tools might miss.
Advanced visual analytics for process insights
Interactive dashboards in Spotfire provide real-time analysis of yield metrics, using:
- Wafer maps to detect spatial yield trends
- Defect density plots to identify anomaly hotspots
- Correlation matrices to uncover relationships between process parameters
Engineers can dynamically filter and drill down into data, quickly identifying root causes of yield loss.
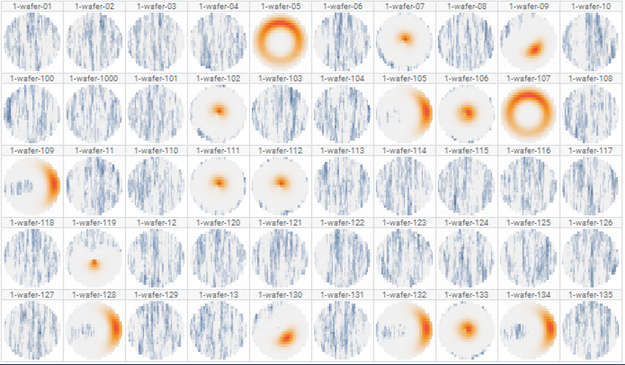
Explore our wafer scratch detection demo to see visual data science in action.
AI-powered recommendations for proactive optimization
Spotfire suggests the best visualizations to conduct advanced analytical techniques such as anomaly detection, predictive modeling, and multivariate analysis. With predictive analytics, manufacturers can anticipate potential yield issues before they escalate, allowing for proactive process adjustments.
Collaborative analytics for cross-functional teams
Spotfire fosters collaboration between yield engineers, process engineers, and data scientists. Shared analytic applications enable teams to make data-driven decisions, reducing time spent on manual analysis and increasing efficiency.
The business impact of Spotfire-driven yield optimization
Beyond technical improvements, Spotfire delivers significant business benefits, helping manufacturers enhance profitability, accelerate decision-making, and maintain continuous process improvement.
Increased profitability through higher yields
Even marginal improvements in yield can lead to significant cost savings, particularly for high-value semiconductor products. Spotfire reduces waste, rework, and production delays, driving profitability.
Faster time-to-insight for critical decisions
By leveraging real-time analytics, Spotfire accelerates problem detection and resolution. Engineers spend less time wrangling data and more time optimizing processes.
Enhanced process control and continuous improvement
Spotfire enables continuous analysis of process stability and yield trends, supporting proactive quality management and long-term process improvements.
The future of yield optimization with Spotfire
As semiconductor manufacturing continues to evolve, yield optimization remains a top priority. The Spotfire® visual data science platform empowers manufacturers to drive higher efficiency, better product quality, and sustained business growth.
Don’t let hidden inefficiencies erode your profits. With Spotfire, semiconductor manufacturers can uncover the insights needed to optimize yield and stay ahead of the competition.
Ready to unlock the full potential of your semiconductor manufacturing data? Discover how Spotfire can help you achieve higher yields at lower costs.