Optimizing processes, reducing costs, and increasing user adoption
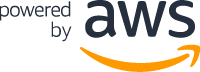
On a daily basis, everyone who uses modern methods to stay connected depends on quality polysilicon. Polycrystalline silicon, or polysilicon, is the primary raw material for the semiconductor and solar industries. It is used to create silicon wafers and other substrates for building a wide range of devices that people use every day, including smartwatches, cell phones, tablets, computers, Internet of Things devices, solar cells, and many others.
Polysilicon is produced through a high-level chemical purification process that involves the distillation of compounds that decompose into silicon at extreme temperatures. Traditionally, polysilicon for electronic products requires impurity levels of less than one part per billion (ppb), though today slightly less pure polysilicon can be used by the solar industry to manufacture solar cells.
Manufacturing raw polysilicon material is fraught with obstacles. Ensuring consistent near-perfect purity levels, taking steps to reduce energy consumption and keeping costs low due to the commoditized nature of the product means industry players must take on a certain amount of risk. These were the main obstacles faced by Hemlock Semiconductor Operations (HSC)
From optimizing production to maintaining market share
In the highly competitive industry of polysilicon manufacturing, Hemlock's ability to consistently produce the highest quality, most reliable polysilicon has positioned it as the partner of choice for many buyers around the world. However, HSC is continuously looking for ways to innovate to remain competitive in the global industry.
Because polysilicon is a commodity, there is little flexibility in pricing. By focusing on reducing manufacturing costs, HSC was able to increase its profitability. "Commoditization in the polysilicon industry requires tight control of our cost structure," said Kevin Britton, program manager at Hemlock Semiconductor Operations.
Optimizing polysilicon production is far more complex than most manufacturing processes. Purity levels of 99.999999999 percent are required to meet most customer expectations. The interaction among process components, must be precisely optimized to maximize yield and plant efficiency. Process variability can lead to higher impurity levels and lower yields. With such a small margin of error, HSC must drive continuous improvement of its manufacturing processes to ensure it is achieving the best possible outcomes.
"Being able to fully utilize the vast volumes of data that we continuously generate became imperative," said Keith Carey, CIO at Hemlock Semiconductor Operations. "We needed to dive deeper into our internal processes to understand how to improve quality while controlling our costs, and take advantage of potential new business models."
To solve the joint operational challenges of cost, quality, and conservation, HSC needed a strategy that would strengthen its long-term profitability and competitive positioning. TIBCO technology was the key to making it a reality.
Controlling costs, maximizing output, and conserving energy
HSC's first focus was on lowering its overall cost structure to ensure long-term price competitiveness. Cost management required analyzing data from each step of the manufacturing process to better understand and quantify the impacts of temperature, pressure, and energy usage in the reactor process.
HSC then was able to re-engineer its manufacturing process by implementing real-time process monitoring and control in order to maximize output, efficiency, and quality.
The next challenge was to address the maximization of product quality. This meant implementing a platform capable of detecting process anomalies. Hemlock's previous infrastructure was a significant obstacle, as much of the company's data was stuck in silos and legacy systems that couldn't keep pace with modern data requirements. But now, when an anomaly is detected, HSC can more readily access data to see precisely which variable may have caused the problem. Once these cause-and-effect relationships are identified, actions are made to prevent process defects from happening again.
While HSC gained a significant handle on its product quality, the market for polysilicon experienced huge growth in recent years, expanding into additional markets requiring different levels of quality based on the nature of the application. For example, the highest quality polysilicon is still used for semiconductors, while solar panels can be made with less pure polysilicon. HSC was able to take advantage of this market segmentation because it had built a data-centric view of its manufacturing processes, allowing it to further optimize its yield by selling the right product to the right market at the right price.
Then came the optimization of energy consumption. HSC's 2020 Sustainability Report reveals how TIBCO helped support the company's sustainability goals and profitability. As stated in the report, "TIBCO Spotfire provides HSC with optimized rollouts and controls for a sophisticated understanding of site processes and energy use. HSC initiated a peak power management program and leveraged TIBCO Spotfire data science to visualize and optimize our performance. Peak power management runs more of our assets during off-peak hours, lowering our demand on the electric grid when consumption is the highest. This program has not only allowed our electric utility to better manage its total demand, but it has also saved HSC approximately $300,000 per month."
"We're Michigan's largest single energy user, and we are pursuing energy efficiency programs. We found TIBCO's Spotfire software to be one of the critical tools to increase energy efficiency. We’re impressed with the results and the data science product that helped us get there," Carey said.
Proactively managing the manufacturing process
The ability to make faster decisions, to detect and prevent product impurities, and to have the agility to pivot production yield based on the quality of the polysilicon was another major focus area. While HSC is an established industry leader, maintaining overall cost competitiveness on the commoditized global polysilicon market is crucial to the continued profitability of its business. Thus, the company couldn’t afford to allow slow decision-making and production bottlenecks to hinder any aspect of cost optimization.
Today, custom data visualizations allow HSC to understand the most granular aspects of its manufacturing processes. The addition of real-time alerting as a complement to that capability has empowered HSC’s workforce to respond to critical production line situations much faster than previously possible. Not only did this solution help HSC lower costs and prevent excess production of waste by alerting personnel right away, it opened the door to projects that improved the manufacturing process.
"With TIBCO, we're connecting data in ways we never could before, which helps us better manage maintenance and plan improvements," said Kevin Britton. "We are able to confirm where we are doing things most efficiently and track our performance, which is a key enabler to being able to improve. This data-driven approach also extends to our continuous improvement process itself.
We're now able to better see, in real time, not only what people are working on, but how our progress tracks to our expectations of how those projects should go. It also allows us to better visualize our capacity and do future modeling for timing of upcoming projects. This is now possible because our tools have advanced to be able to combine fairly complex data from multiple sources for visualization."
By allowing HSC to move from a reactive to a more proactive management of the manufacturing process, TIBCO helped the company discover new business opportunities.
"We're moving from archaic, static data to more intuitive, realtime data," Carey said. "We needed to be able to look at our internal information to understand costs in more detail and bring in external information so we could take advantage of potential new business models, such as offering excess material on the spot market."
A technology foundation to reinforce industry leadership
HSC's focus on cost began with a smaller-scale implementation of TIBCO Spotfire analytics. The solution provided HSC with a real-time visual representation of gaps in the manufacturing process. When anomalies occurred, it can quickly pinpoint which piece of equipment needed troubleshooting and alert company personnel. It can also be used to perform what-if scenario analyses to model the impact of process changes in near real-time.
While intelligent data analytics enabled greater control over HSC's complex manufacturing and operational processes, these elements would not be nearly as robust without a universal connectivity of HSC’s systems, processes, machinery, and more. That's where TIBCO integration came into play. HSC began with several important analytic requirements that ultimately revealed how the ubiquitous connectivity of data was critical to a cleaner and more comprehensive view of its business.
"We had six or seven use cases for integration that we identified and wanted to roll out over time," Carey said. "The first one was manufacturing integration: how do we connect the shop floor to the ERP system and business system? That has generated lots of data for us. We’re not only analyzing systems into which we previously had limited visibility, we better understand inventory levels, and more. It’s a platform that we can grow into as our business needs evolve. That’s another reason for our investment in TIBCO."
HSC realized that strong integration across systems empowered it with even more information to which it was able to extend the impact, usefulness, and breadth of its analytics. As market dynamics, business models, and customer demands were changing, so too was HSC’s ability to provide more compelling analytic insights that enabled it to expand with additional use cases, in a scalable and sustainable way, with greater confidence.
The success of HSC’s initial efforts also led to an expanded use of the TIBCO Connected Intelligence platform. TIBCO powers Hemlock's Center of Excellence, which lays the foundation for its integration program and SAP S4/HANA system. The Center of Excellence brings together myriad integration, analytics, and data management tools that work together to strengthen HSC's underlying architecture. It provides advanced analytics capabilities, including data science and virtualization, streaming analytics, and other self-service tools.
This integration with SAP S4/HANA means that information can be replicated in real time and exposed to a wider HSC user community through a series of calculation views. TIBCO simplifies the delivery and transportation of information in a timely manner, which results in large dividends for HSC. Beyond being the foundational tool beneath HSC's infrastructure, TIBCO also lends its expertise and ongoing support to ensure continued success with the platform. HSC can now handle a variety of use cases—including manufacturing integration, B2B, and hosting APIs—that allows its customers to consume its data in a safe and secure environment.
Maximizing the value of all data, across all roles
As a manufacturer of one component in a longer supply chain, HSC has several partners with whom sharing data is a valuable capability.
"TIBCO has advanced the way we provide detailed business and operational data to our end users without them having to wait. Self-service capability is a key component of our IT strategy," said Carey.
With TIBCO, HSC can consume and analyze multiple years of data, compared to previous spreadsheet-based data-wrangling methods that were limited to just 90 days of data.
"We now have visibility into processes that were very difficult to see before and can pursue answers to the really complex questions that enable us to optimally tune each process,” Britton said.
Because the TIBCO Connected Intelligence platform is live and dynamic, it allows teams to come together to solve problems and perform root cause investigations*#8212;all enabled by real-time data. Most importantly, it has helped HSC foster a data-driven culture with analytics that can be accessed in seconds. This cultural shift has changed the way the company sells ideas, solves problems, and brainstorms solutions. TIBCO has become the catalyst toward shifting to a data-driven environment where solutions are made alongside data, not just supported by data. TIBCO solutions have become an integral part of the company, routinely being used in meetings, discussions, and presentations.
"Now, we collaborate as one team and dig into the data in real-time to solve problems," Carey said. "Enabled by data and the TIBCO platform, the speed at which we learn and fail fast is significantly different from the past."
The next phase of the all-in with TIBCO plan
When the polysilicon market began experiencing disruption, HSC knew it had to transition to maintain its leadership. TIBCO’s Connected Intelligence platform helped HSC embrace the disruption by modernizing its infrastructure and providing the agility it needed to make faster, smarter decisions. From the very beginning, partnering with TIBCO helped HSC understand how to optimize numerous aspects of its business.
HSC has several capabilities in mind for the future, including a more robust master data management system, a manufacturing digital twin, the expansion of its data science applications, and an improved responsiveness to real-time alerts enabled by data streaming. In the next few years, HSC hopes to make its data AI-ready and consumable for B2B end users.
From the ability to visualize and optimize production costs to maximizing product quality and quantity and helping create a more reliable workspace, HSC is confident in its partnership with TIBCO and believes that its future lies with TIBCO.
"The speed of our development and the robustness of our solutions is going to be key to HSC’s future. The TIBCO Connected Intelligence platform is really going to help us," Carey said. "Our decision to partner with TIBCO has been validated time and again; we picked the right tool and the right company for our culture. We’re looking forward to what we do in the future, especially with our integration in the next phase of our all-in with TIBCO plan."
$300K
savings per month
In electricity consumption via analytic-driven asset utilization
With TIBCO, we're connecting data in ways we never could before, which helps us better manage maintenance and plan improvements. We are able to confirm where we are doing things most efficiently and track our performance, which is a key enabler to being able to improve.
Kevin Britton
Program Manager
Hemlock Semicondutor Operations
Featured resources
Hemlock Semiconductor Operations (HSC) is the largest producer of polysilicon in the United States.
Hemlock Semiconductor
Global producer of polycrystalline silicon for semiconductors, Hemlock Semiconductor needed to accelerate process optimization and eliminate cost. With Spotfire®, Hemlock achieved centralized, self-service, governed analysis; revenue gains; cost savings; and more.